By Claire Ferris-Lay www.constructionweekonline.com
When Depa won the contract to fit out a major portion of the interiors of the Burj Khalifa, the world’s tallest skyscraper, in 2006, the Dubai-based firm was under no illusion that the multimillion-dollar project would be one of its most challenging yet.
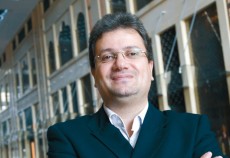
Depa, the world’s largest interior fitout contractor, regularly works on large scale projects such as luxury hotels, airports, cruise ships, malls and offices.
But completing the Burj Khalifa at the same time as helping install the interiors for another of Dubai’s major projects, the Metro, was one of its toughest tests to date.
“We never expected it to be an easy project; after all, this is the world’s tallest tower and we always knew it would be a challenging project,” says Nadim Akhrass, managing director of operations for Depa.
“It’s been challenging since the first day but the bright side is that the world will soon be able to see the fruits of three years of very hard work.”
Many of the problems centred around the logistics of transporting thousands of tonnes of materials up to some of the tallest residential apartments in the world.
Then there was dealing with the sheer size of Depa’s labourforce. While the firm had 150 staff working in the office from the beginning of the project, during the peak of construction, which continued for more than a year and a half, the firm employed more than 2,400 labourers onsite.
“There was a logistical challenge working on the Burj Khalifa given its huge height. To move hundreds of workers up hundreds of floors to the final work location, to feed them, take care of their sanitary facilities and get them back to buses at the end of the day is a very challenging process,” admits Akhrass.
To overcome the time constraints, Depa ensured that all transportation of the materials, which included a staggering 8,000 tonnes of marble imported from Italy, 100,000 square metres of parquet flooring and 8,500 timber doors, was completed at night, using a dedicated lift. This move allowed labourers working the day shift to concentrate solely on the materials’ installation.
Depa won the ‘S06’ contract to fit out all of the building’s residential apartments in April 2006. As part of the mandate, the firm has completed the interiors of 900 apartments between floors 19 and 107 on the middle tiers, which are located above the Armani hotel and below the office space on the top section.
In addition to kitting out all of the interior walls, flooring, wood paneling and the joinery and stone work for the kitchens and bathrooms in all of the apartments, Depa was also responsible for four amenity floors.
At the height of Dubai’s five-year real estate boom, the cost of an apartment in the Burj Khalifa complex reached as much as $3,540 per ft ², topped only by Nakheel’s now-delayed Trump Tower on the Palm Jumeirah.
Despite the estimated 50% decline in Dubai’s house prices in the wake of the global financial crisis, the area has managed to hold its prices better than most.
Akhrass says end users will be more than satisfied with the end results of the firm’s three years of hard work.
“The apartments are beautiful. While the contractors had a tough time building them, the end users will enjoy very high-end, quality apartments,” he says confidently.
Each apartment features a significant amount of wood. While 90% of the apartments are fitted out with a modern design using wenge wood, the other ten percent feature a more classic design that focuses on timber veneers and parquet flooring. In the communal areas, 8,000 m² of rose wood was procured from Germany and Brazil.
Ahkrass says that if it wasn’t for Depa’s subsidiaries, Depa Industrial Group and Singapore-based Depa Design Studio, taking direct control over the timber finishes and the joinery work, it wouldn’t have been able to complete the project to the specified date.
“If we had not had any control over those companies, which are vertically integrated into the Depa business, we wouldn’t have been in any position to complete the project because it’s so timber-oriented,” he explains.
“We are talking about kilometers of skirting, hundreds of thousands of metres of veneer from Brazil and Germany and a vast amount of rose wood, which is very expensive, that is used in the lift lobbies corridor walls and amenities. When visitors get out of the lift, they won’t feel like they are in a residential building. It’s more of a high end hotel finish.”
The final interiors were the second set of designs following a decision by the project’s developer Emaar to upgrade the finishes in June 2008.
This decision, which Akhrass concedes was correct in hindsight, set the completion of the interiors back slightly.
The changes are likely to affect the overall cost of Depa’s work. In April 2007, the firm signed a $118m financing agreement with Mashreq and HSBC to fund the project. Fortunately, says Akhrass, materials for the project were procured before the significant rise in commodities prices during 2008.
“[The rise and fall in commodity prices had] no impact at all because we procured 100% of the materials a long time ago, at 2006 and 2007 prices.”